Quartz Processing Plant Compressed Air Piping System
Providing a North Carolina quartz processing plant with contaminant-free air with a lifecycle many times greater than steel pipe—ultimately saving the plant thousands in maintenance, repair, and replacement costs.
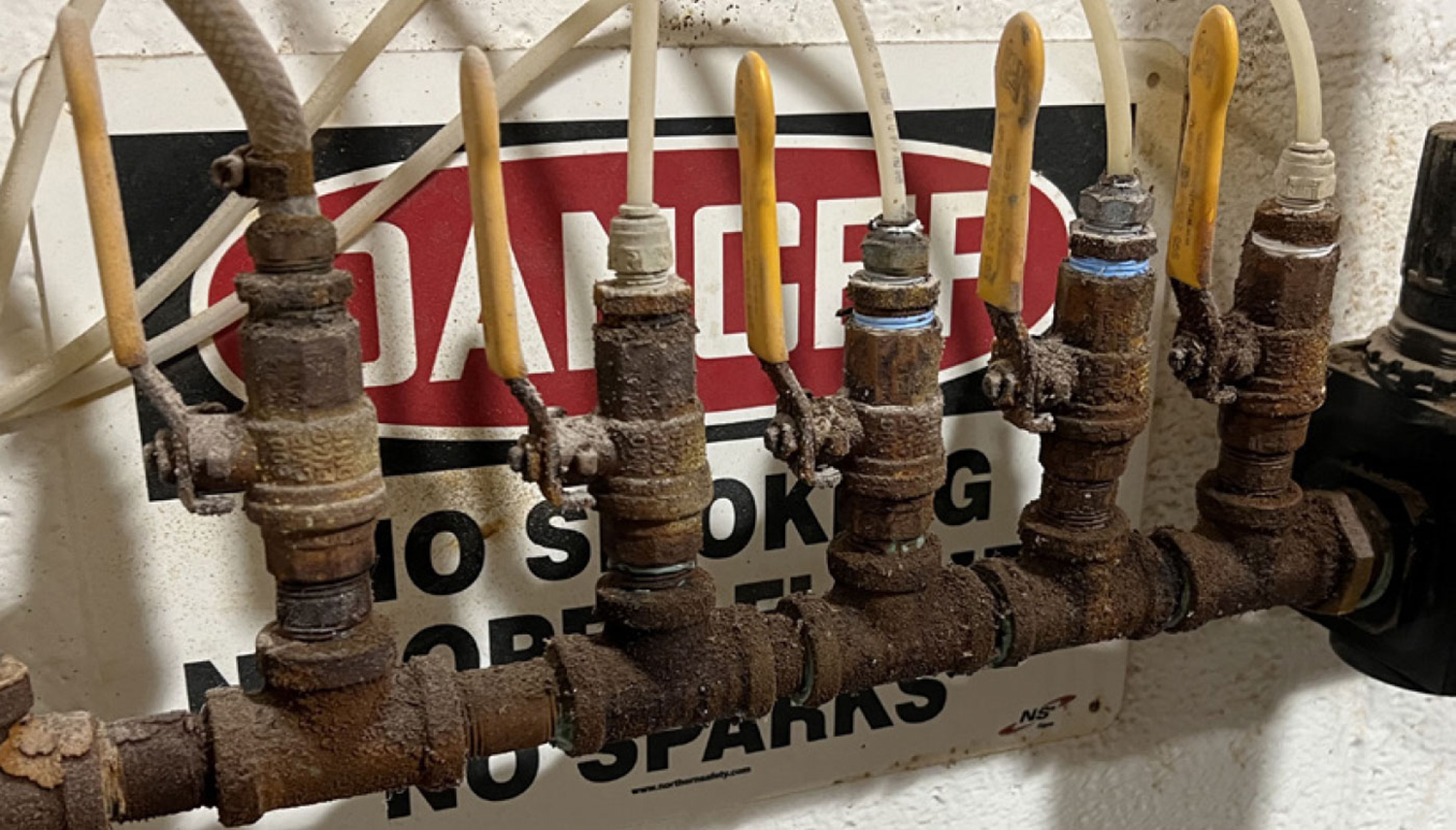
Download Chemical Scrubber Piping Replacement:
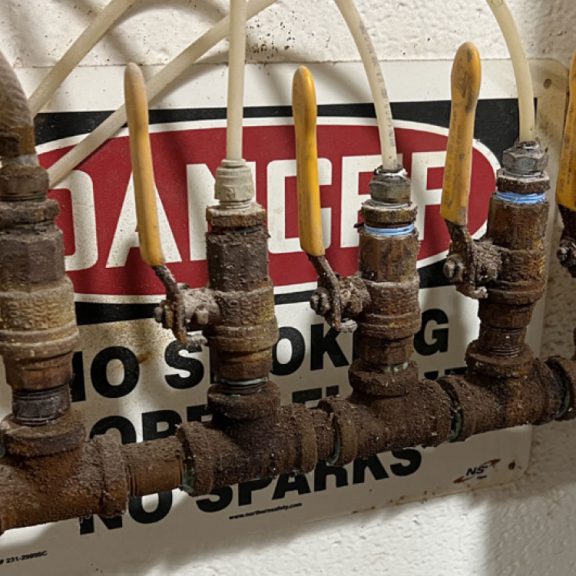
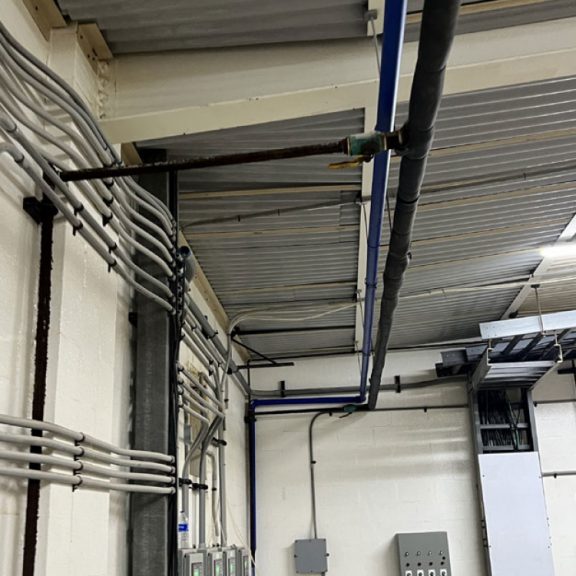
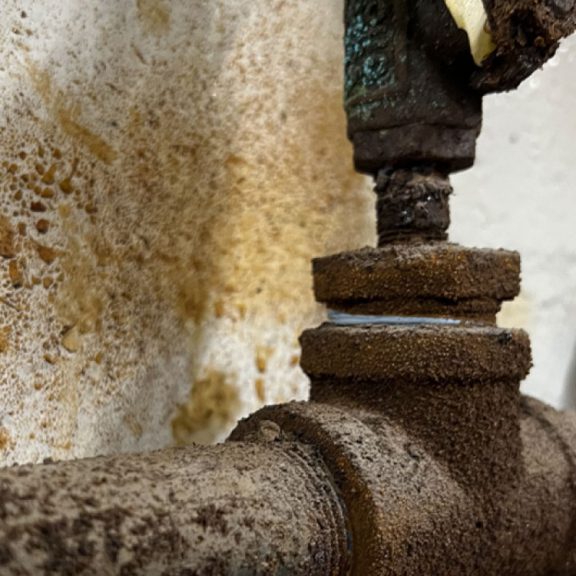
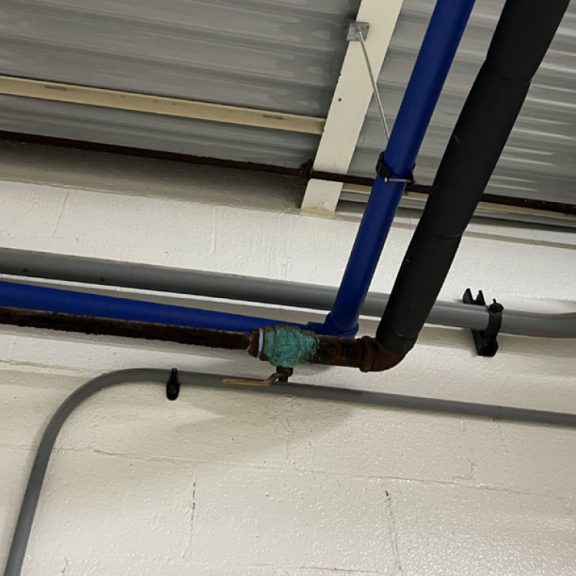
PRODUCTS USED
Asahi Air-Pro® PE100 Compressed Air Piping System
CHALLENGE
As a result of the plant’s corrosive environment, the black steel compressed air piping system was damaged. Consequently, rendering leaks and contamination throughout the air system.
SOLUTION
Ultimately, to replace the black steel with an industrial thermoplastic engineered for compressed air applications.
PRODUCT ADVANTAGES
- Rapid technical and commercial response
- Extensive inventory of corrosion-resistant pipe and fittings
- Socket and butt fusion joining expertise and equipment
PROJECT SUMMARY
To explain, the compressed air system of a North Carolina quartz processing plant features hundreds of feet of pipe ranging from 1/2″ to 4″ in diameter. The system is exposed to the plant’s internal environment on every floor of the facility. Therefore, the chemicals introduced into the air from the plant’s reactors are in constant contact with the pipe for almost its entire run.
Together, the black steel pipe and corrosive environment are incompatible in the long term. Consequently, this incompatibility causes external corrosion, resulting in leaks and contaminating the compressed air within.
Ferguson Industrial Associates recently supplied this industrial plant with a thermoplastic solution for a failing chemical scrubber system. After success in that replacement, the plant team knew they could rely on us to identify the right product to replace the black steel.
What was the compressed air piping system used in the quartz processing plant?
Our experts selected Asahi Air-Pro® PE100 Compressed Air Piping System for the following reasons:
- Excellent chemical compatibility both inside and out to handle conditions of service without being compromised
- Lightweight for ease of installation and use of existing supports
- Socket and butt fusion joining system for maximum joint integrity
- High-pressure rating capability
- Minimum 50-year expected useful life in the application
Because we have a team dedicated to Thermoplastics, we offer in-depth knowledge of industrial processes. Therefore, we understand both the challenges and have expert insight into the materials that are required to overcome those challenges. Our Ferguson Industrial team worked to significantly reduce the lead time on replacing the black steel system. Beyond the material selection process, we also facilitated the delivery and demonstrated the joining process for the product to maximize the system’s chances of success.
The new system, immune to corrosion from the environment, provides the plant with contaminant-free air. Furthermore, its lifecycle is many times greater than steel pipe—ultimately saving the plant thousands in maintenance, repair, and replacement costs.
View Similiar Case Studies
Our Automated Supply Program (ASP)—an advanced, indirect material supply chain software—and our proven processes to control their MRO indirect spending reduced the total cost of ownership by 24.2% in the first year post-integration.
Our associates identified an opportunity to use our online Automated Valve Configuration Tool to build out exactly what the customer needed. In less than 15 minutes, our flow control experts were able to walk the customer through the process of configuring an FNW® automated ball valve package.
Expert technical assessment, material selection, and supply of Polypropylene at a quartz processing facility in North Carolina.