Refinery Limitorque Actuator Refurbishment
Maintaining close partnerships and our team’s willingness to go the extra mile helped us realize significant costs and get the plant back to running.
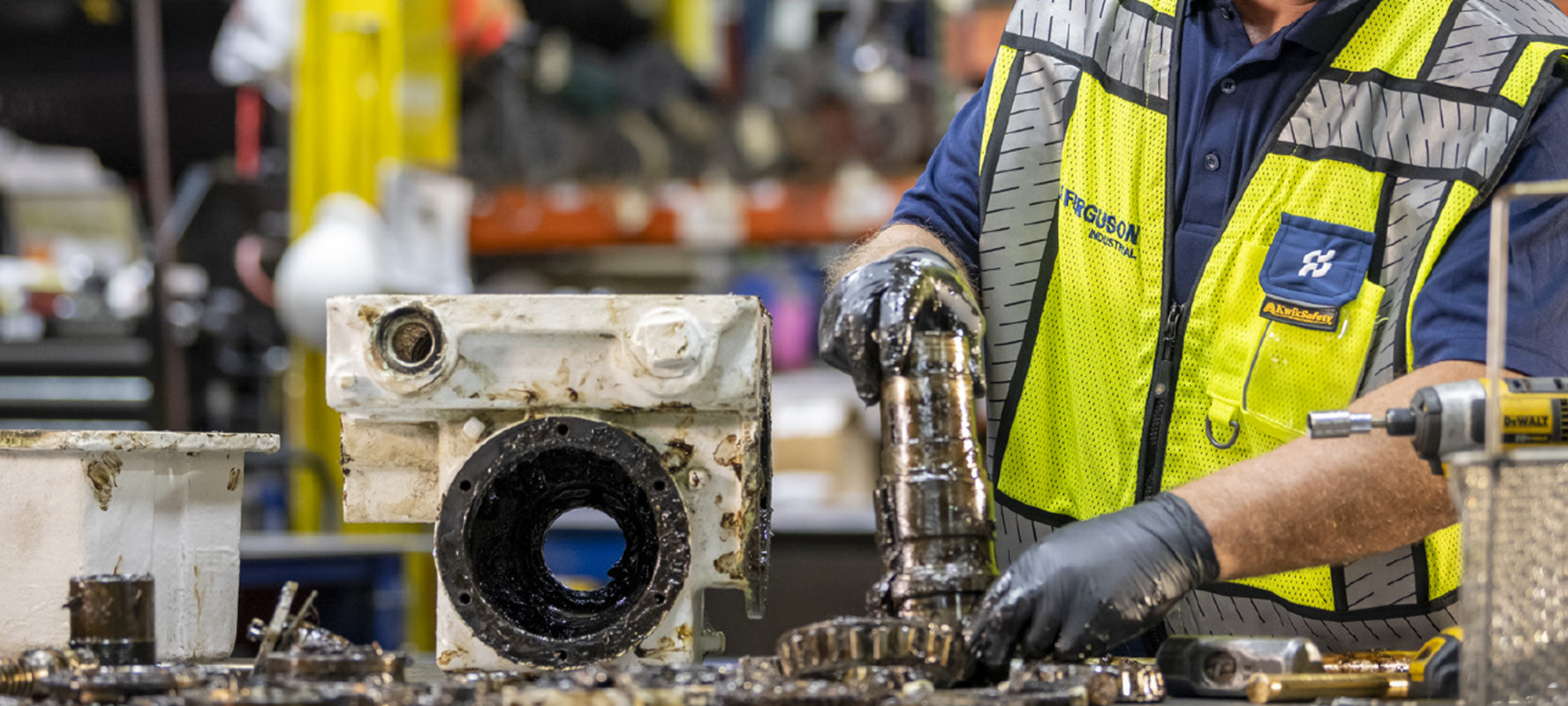
Download Refinery Limitorque Actuator Refurbishment
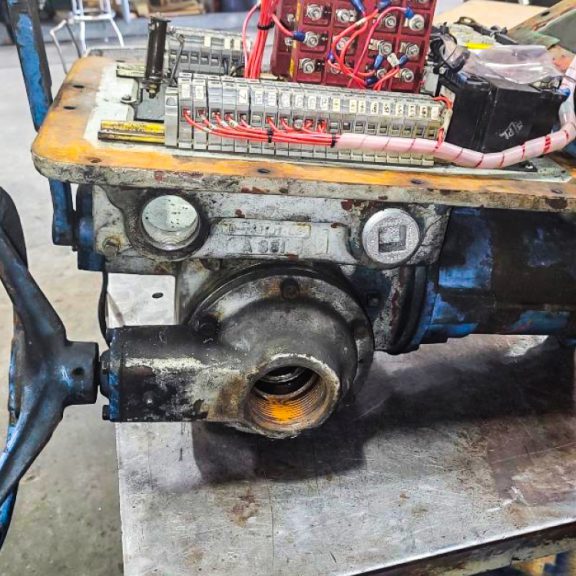
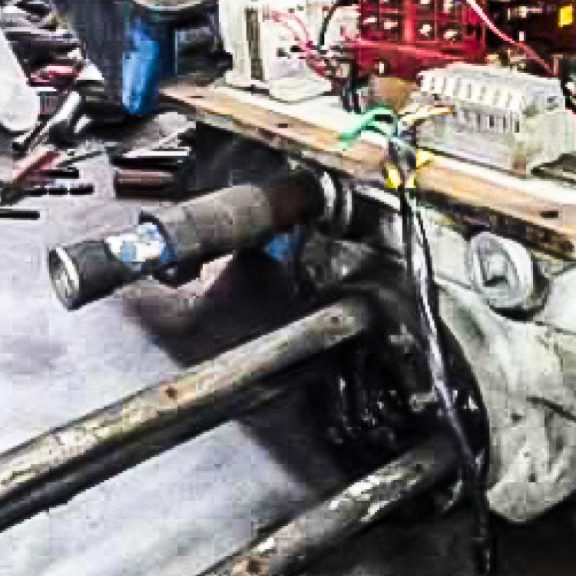
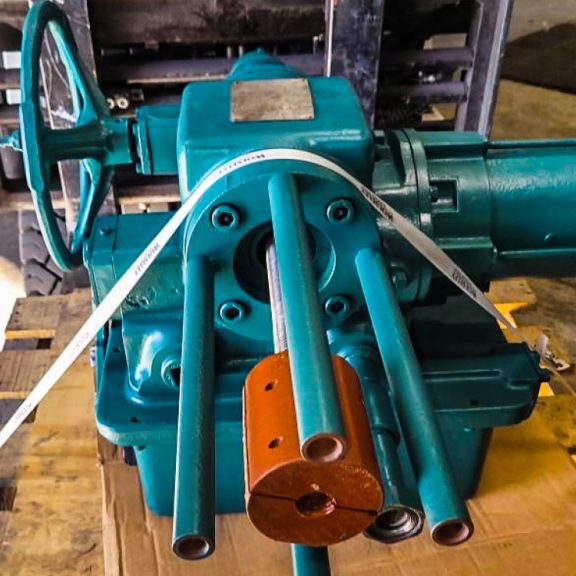
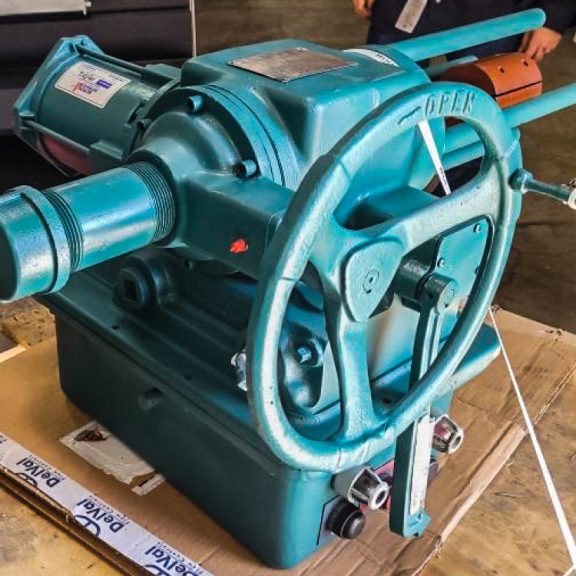
PRODUCTS USED
Limitorque® SMB Actuator
CHALLENGE
The suboptimal performance of an actuator in critical control valve service threatened to result in 35 weeks of lost opportunity costs due to waiting for a replacement.
SOLUTION – Actuator Refurbishment
Refurbish the misfunctioning actuator with our advanced technology and expertise at our Limitorque Blue Ribbon-certified facility.
OUR ADVANTAGES
- Expert service in Limitorque Actuator refurbishment
- Manufacturer-certified repair
- Immediate and effective technical response
- Large in-stock selection of crucial repair parts
- Significantly reduced lead time
Why is actuator refurbishment essential for refinery operations?
Project Summary
When an actuator in critical control valve service at a leading downstream energy plant began to perform below expectations, the obvious option was to replace it. However, a new actuator couldn’t arrive onsite for 35 weeks. Consequently, roughly nine months of substandard operations would cost hundreds of thousands—if not millions—in lost opportunity costs.
To minimize downtime, we recommended our actuator repair services as the best path forward. Firstly, the misfunctioning actuator was shipped from their facility to our Limitorque repair facility in Chicago, IL. Then, our team of technical experts disassembled the product, cleaned the parts, and furnished it with the necessary new components. As a result, we restored the actuator to peak operation.
Because our facility stocks a wide range of repair parts for various types of actuators and our technicians are certified by the manufacturer, we were able to refurbish the product and get it shipped out within 36 hours of receipt.
Our commitment to maintaining close partnerships with vendors like Limitorque and our team’s willingness to go the extra mile for our customers on the weekend helped us realize significant cost savings. And, most importantly, get the plant back to running at full speed.
To discuss actuator refurbishment or to learn more about our Limitorque Blue Ribbon-certified facility, contact us today.
View Similiar Case Studies
Our Automated Supply Program (ASP)—an advanced, indirect material supply chain software—and our proven processes to control their MRO indirect spending reduced the total cost of ownership by 24.2% in the first year post-integration.
Our associates identified an opportunity to use our online Automated Valve Configuration Tool to build out exactly what the customer needed. In less than 15 minutes, our flow control experts were able to walk the customer through the process of configuring an FNW® automated ball valve package.
Expert technical assessment, material selection, and supply of Polypropylene at a quartz processing facility in North Carolina.