Exceptional Service Cuts Lead Time By More Than 60 Percent
Our quick response and commitment to exceptional service cut lead time by more than 60%, resulting in reduced downtime and millions in customer savings.
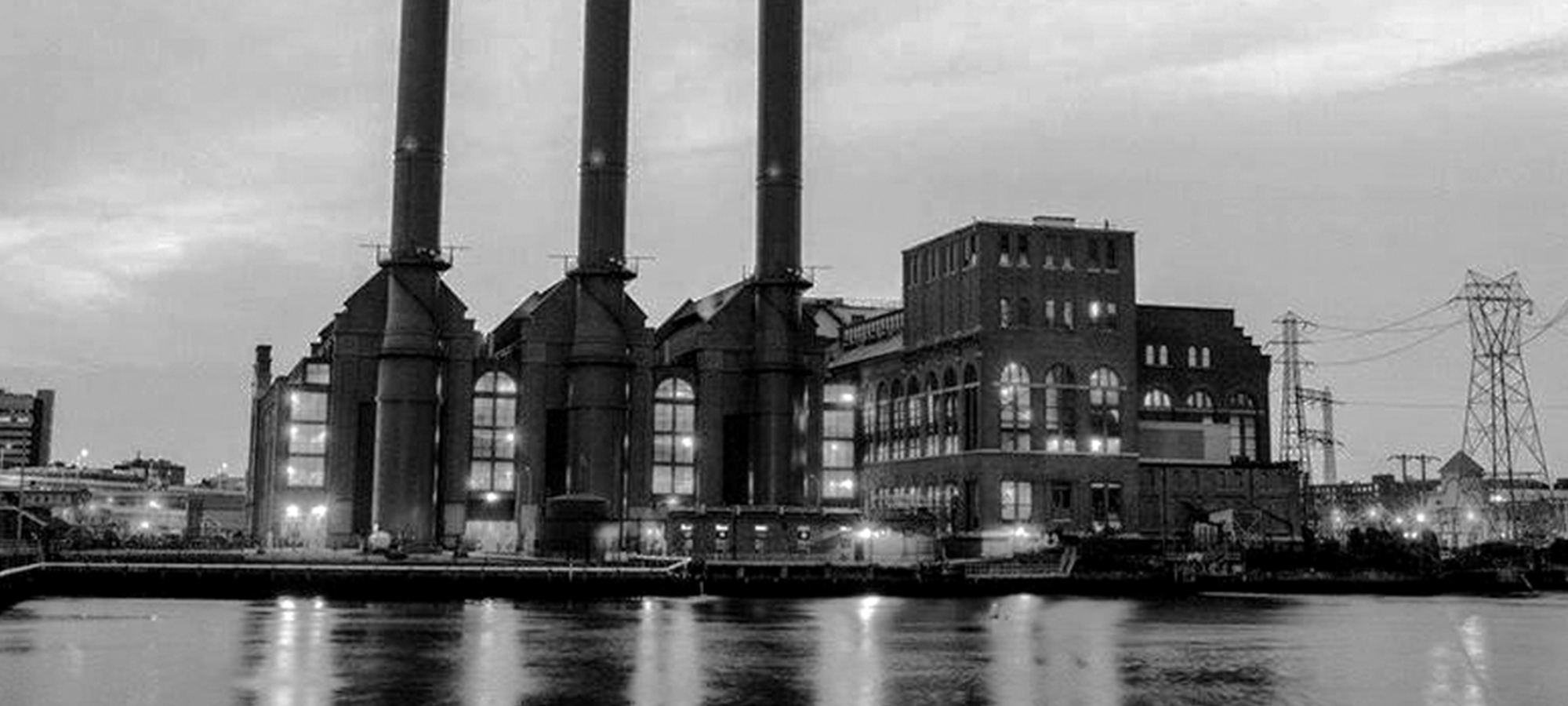
When an unfortunate situation becomes a dire one, it helps to have a reliable partner on speed dial who can source industrial products fast. Especially a team that’s up for a challenge.
A power generation company suffering from issues with an HRSG boiler tube needed a replacement. Due to the tube’s requirements and specifications, the company was having a difficult time sourcing it on their own. Fortunately, as a result of being in the industry for decades and building strong relationships with our suppliers, sourcing hard-to-find products is one of Ferguson Industrial’s specialties. Unfortunately, shortly after contacting us, the tube ruptured. This forced a shutdown in one of the plant’s four boilers.
We Help All Of Our Customers Source Industrial Products Fast
Previously, the company had benefited from Ferguson Industrial’s agile solutions in both emergencies and routine matters. So, when disaster struck, they hit their speed dial, knowing we could help source industrial products fast.
As usual, our support team jumped into action and responded immediately. Within 24 hours we sourced, acquired, and delivered the HRSG boiler tube.
With our assistance, the downed boiler was operating at normal capacity within 36 hours of the initial failure. As a result, our customer saved millions of dollars in potential lost power generation and revenue.
View Similiar Case Studies
Our Automated Supply Program (ASP)—an advanced, indirect material supply chain software—and our proven processes to control their MRO indirect spending reduced the total cost of ownership by 24.2% in the first year post-integration.
Our associates identified an opportunity to use our online Automated Valve Configuration Tool to build out exactly what the customer needed. In less than 15 minutes, our flow control experts were able to walk the customer through the process of configuring an FNW® automated ball valve package.
Expert technical assessment, material selection, and supply of Polypropylene at a quartz processing facility in North Carolina.