Chemical Plant Scrubber Duct System Replacement
Expert technical assessment, material selection, and supply of Polypropylene Chemical Scrubber Piping Replacement at a quartz processing facility in North Carolina.
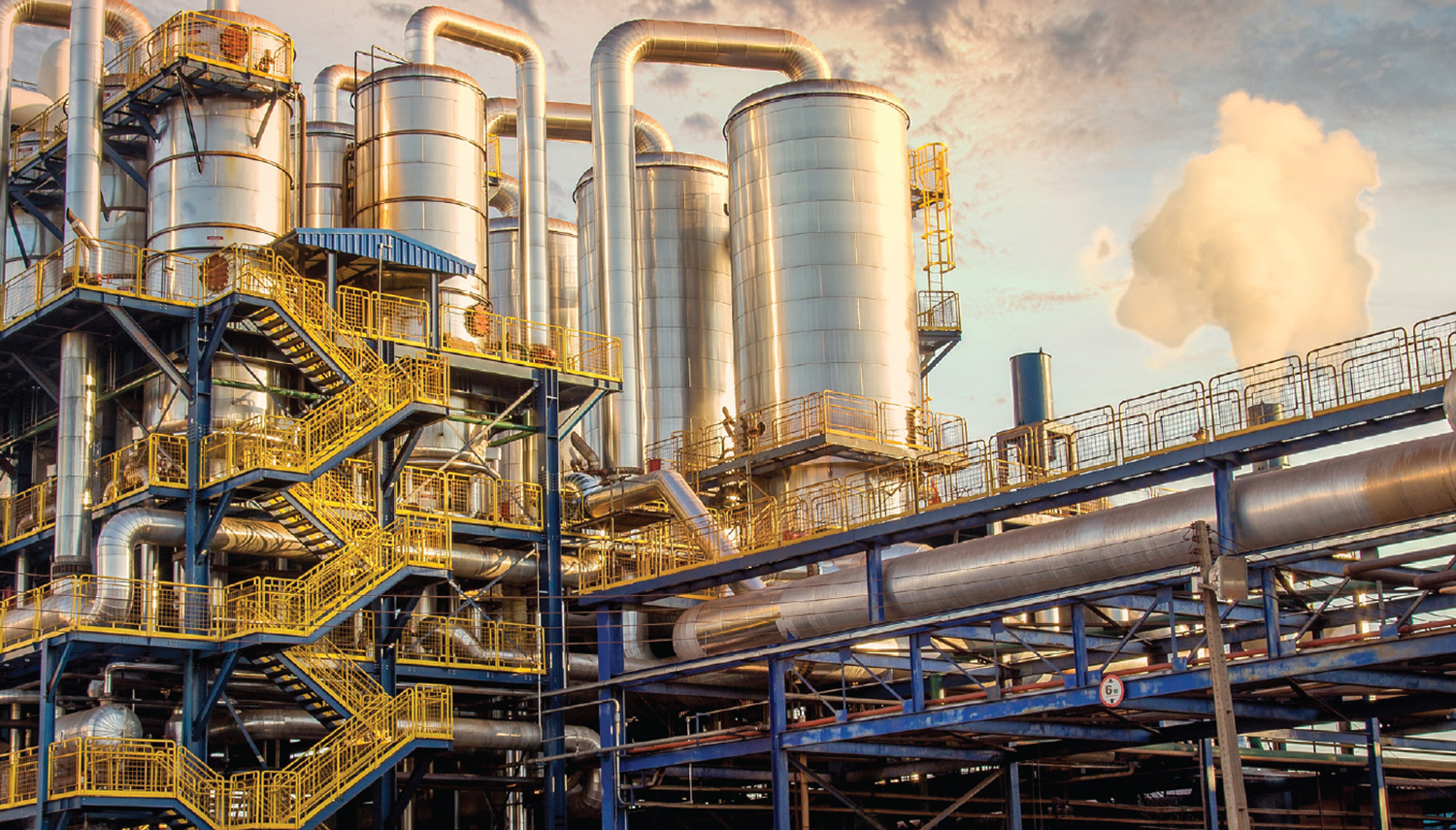
Download Quartz Processing Plant Compressed Air Piping System
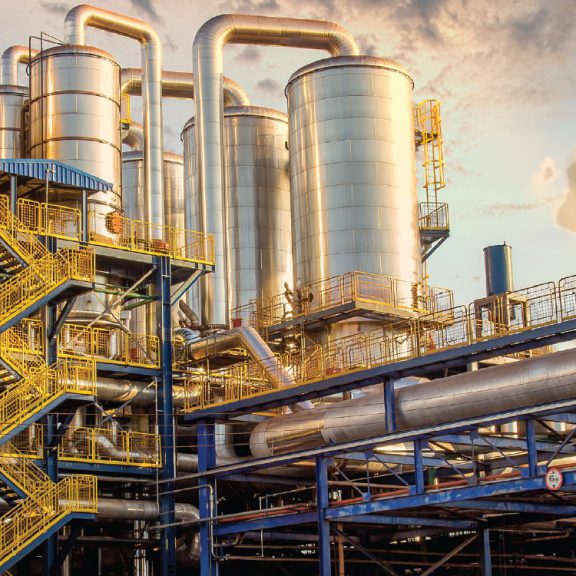
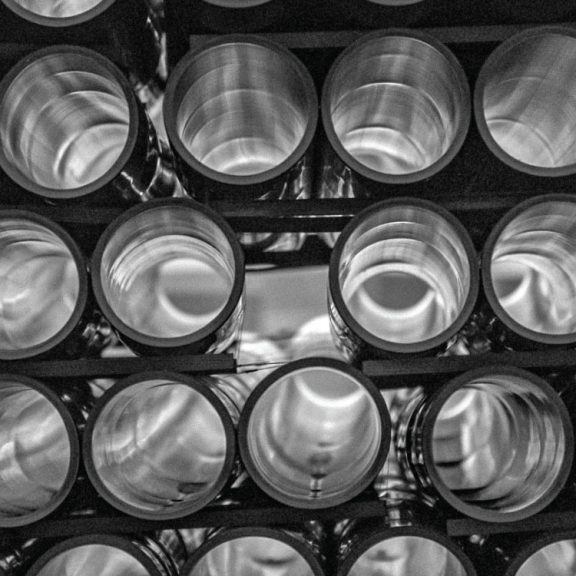
PRODUCTS USED
Polypropylene
CHALLENGE
The aging PVC piping in the plant’s chemical scrubber piping system needed to be replaced with an easy-to-install alternative. The solution needed to withstand internal/external environments and corrosive media.
SOLUTION
Expert technical assessment, material selection, and supply of Polypropylene Chemical Plant Scrubber Duct Replacement pipe.
PRODUCT ADVANTAGES
- Rapid technical and commercial response
- Extensive inventory of corrosion- and weather-resistant pipe and fittings
- Butt fusion joining expertise and equipment
- Equipment training services
PROJECT SUMMARY
At a quartz processing facility in North Carolina, the fume exhaust and scrubber system supporting an acidic process was failing. The pipe—thin-wall PVC ducting, up to 12″ in diameter—was leaking at the joints. Furthermore, the material had become brittle. Because of the material’s decrease in integrity, it posed hazards to those working inside the plant. In addition, it also impacted the environment immediately outside the plant. The system consisted of hundreds of feet of pipe, both inside and outside the facility.
What is the best solution for chemical scrubber piping replacement?
The plant team contacted Ferguson Industrial for a solution, which our team provided within days of the initial ask. Our product specialist determined that Polypropylene would meet the project’s specifications and contribute additional long-term benefits to the system.
We chose an advanced, thin-wall Polypropylene because of its chemical compatibility to handle the conditions of service, its lightweight for ease of installation and compatibility with existing support infrastructure, and butt fusion joining for maximum joint integrity to limit expansion and contraction.
Because the piping system exists both inside and outside the plant, our product specialist selected a product with a UV inhibitor to reduce the effects of sun and weather on the external portions of the system.
Our team provided samples of Chemical Plant Scrubber Duct Replacement. Then, we demonstrated the joining procedure for the customer to grant them peace of mind regarding its efficacy before they committed to the product.
This solution helped the customer save on material costs for the replacement and will help reduce labor and maintenance for the lifetime of the system.
View Similiar Case Studies
Our Automated Supply Program (ASP)—an advanced, indirect material supply chain software—and our proven processes to control their MRO indirect spending reduced the total cost of ownership by 24.2% in the first year post-integration.
Our associates identified an opportunity to use our online Automated Valve Configuration Tool to build out exactly what the customer needed. In less than 15 minutes, our flow control experts were able to walk the customer through the process of configuring an FNW® automated ball valve package.
Providing a North Carolina quartz processing plant with contaminant-free air with a lifecycle many times greater than steel pipe—ultimately saving the plant thousands in maintenance, repair, and replacement costs.