Customized fabrication of HDPE pipe for fittings, components and structures
We excel with the design, engineering assistance and custom fabrication of HDPE pipe and fittings that provide the flexibility to pipe systems that meet the needs of your application.
With our experience in design and fabrication of specialty HDPE products, we provide solutions and HDPE pipe fusion techniques applicable for custom fabricated fittings, components and structures to meet unique or specialized design specifications. Along with our extensive fleet of McElroy HDPE pipe fusion equipment, we have certified factory-trained fusion technicians and trainers who are capable of providing on-site HDPE fabrication training.
Our fabrication facilities work with HDPE pipe to build pipe assemblies, fittings, spacers, tanks, manholes, spillways and other specialty items.
Learn more about our HDPE Pipe Fusion and Fabrication Services.
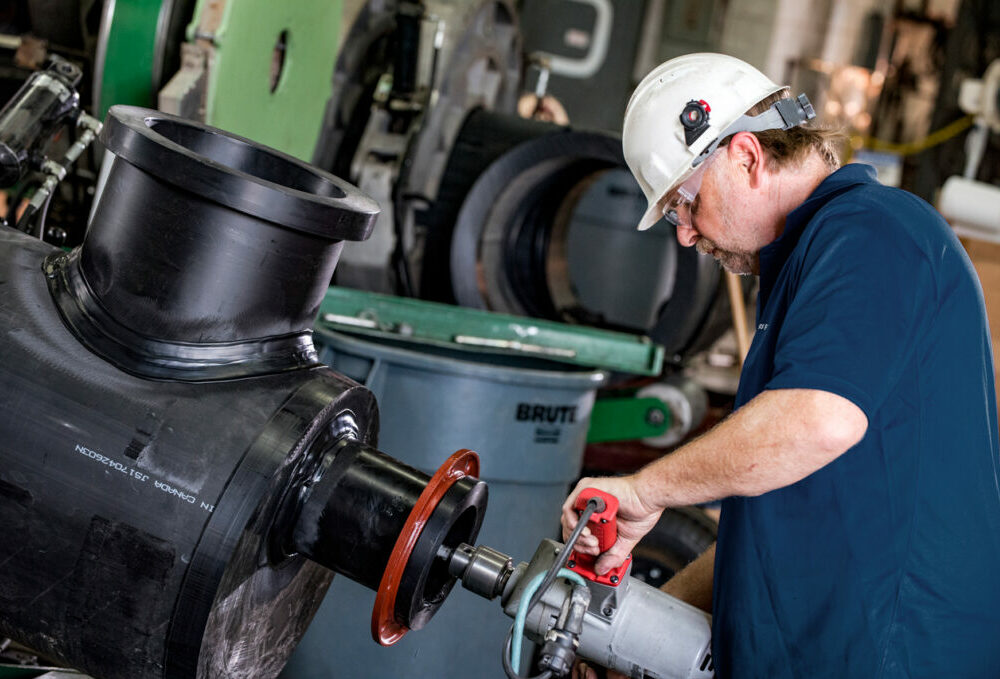
Fusion Services
In addition to our expansive offering of quality HDPE products and ability to customize fabricated systems for a wide range of applications, we also serve customers across the industrial market with fusion services. From pipe fusion machines and pipe fusion accessory rentals to on-the-job training, we are your complete source for HDPE pipe fusion equipment solutions and support.
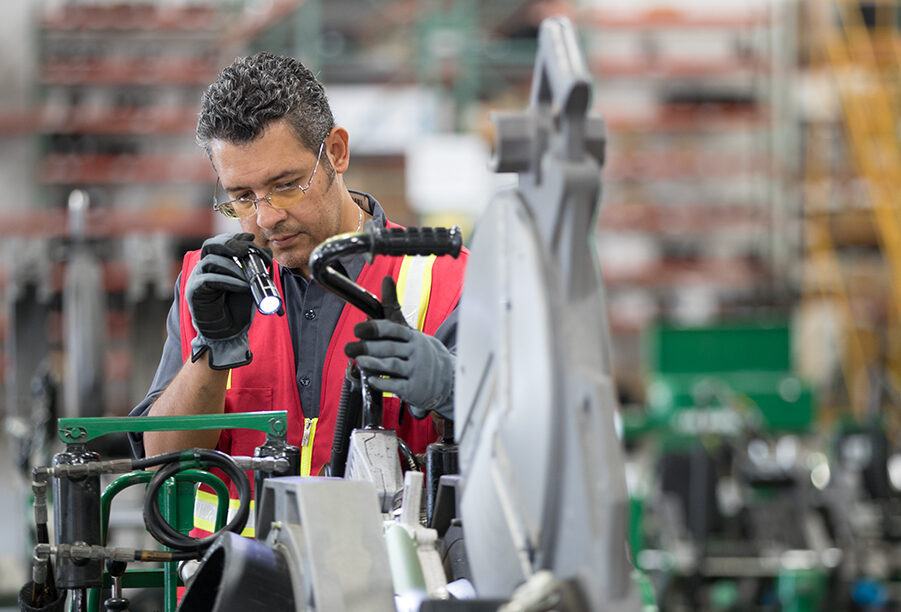
Fusion Machine Rental, Sales and Repair
With our national footprint, we can deploy the appropriate McElroy fusion equipment and HDPE pipe needed to any jobsite nationwide.
We offer:
- A large fleet of McElroy fusion equipment for rental and sale.
- Authorized equipment repair facilities located throughout the U.S.
- Equipment that is part of certified McElroy rental program ensuring highest quality
Our equipment offering includes:
- Rolling and TracStar track machines
- ½” Through 65” McElroy fusion machines
- Legacy and iSeries fusion machines
- Dataloggers
- Socket welders
- Electrofusion processors
- Extrusion welders
- Sidewall fusion machines
- De-beading tools
- Generators
- Factory-certified service and repair
HDPE Fusion Equipment
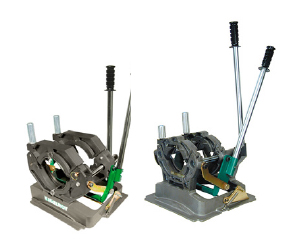
PIT BULL 14 & 26
These models are compact and lightweight with size ranges from 1″ through 6″.
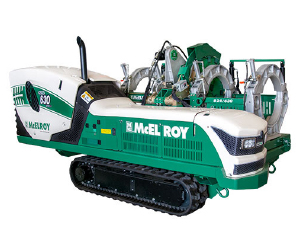
TRACSTAR 630
Fuses 14″ through 24″ pipe. This is a track mounted machine that has its own generator.
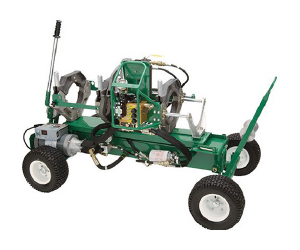
Rolling 28
Fuses 2″ through 8″ pipe. This is an electric hydraulic machine that uses a 3.5kVA/3.2kw generator.
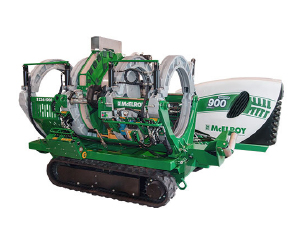
TRACSTAR 900
Fuses 12″ through 36″ pipe. This is a track mounted machine that has its own generator.
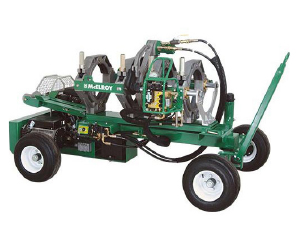
ROLLING 412
Fuses 4″ through 12″ pipe. This is an electric hydraulic machine that uses a 3.5kVA/3.2kw generator.
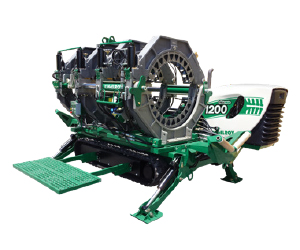
TRACSTAR 1200
Fuses 12” through 36” pipe. This is a track mounted machine that has its own generator.
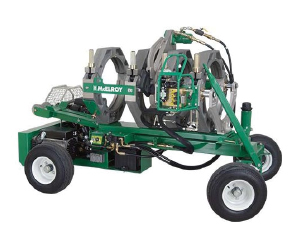
ROLLING 618
Fuses 6″ through 18″ pipe. This is an electric hydraulic machine that uses a 3.5kVA/3.2kw generator.
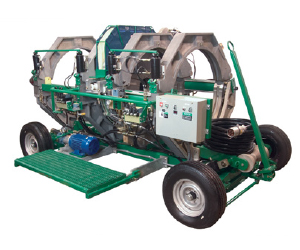
MEGAMC 1648
Fuses 16″ through 48″ pipe. This machine requires a 70kw generator.
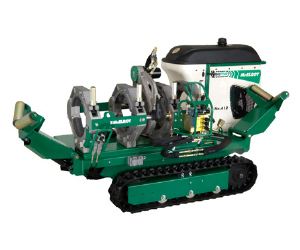
TRACSTAR 412
Fuses 4″ through 12″ pipe. This is a self contained machine that is track mounted and has its own generator.
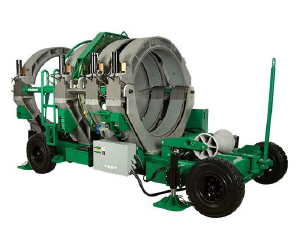
MEGAMC 1600
Fuses 20″ through 65″ pipe. This machine requires a 85kw generator.
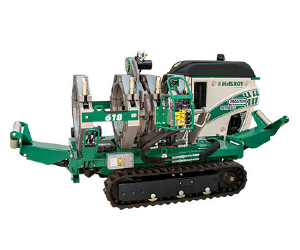
TRACSTAR 618
Fuses 6″ through 18″ pipe. This is a self contained machine that is track mounted and has its own generator.
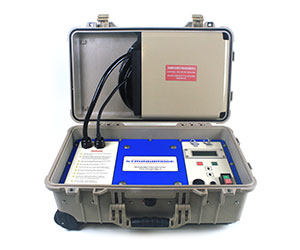
ELECTROFUSION WELDER
Joins bar coded PE and PP pressure fittings in the range of 8v to 48v. It will recognize and read extended traceability bar codes found on fittings pipe and accessories.
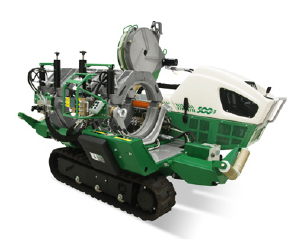
TRACSTAR 500
Fuses 6″ through 20″ pipe. This is a self contained machine that is track mounted and has its own generator.
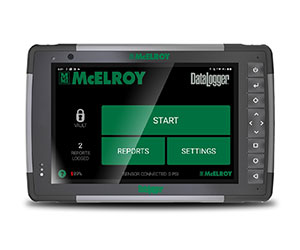
DATALOGGER
Captures GPS locations, jobsite photos, barcoded details from pipe and fittings, and uploads the collected data from the field via wireless connections.
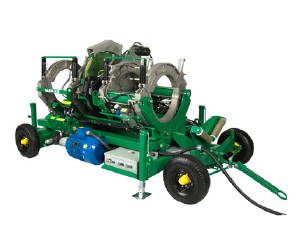
MEGAMC 824
Fuses 8″ through 24″ pipe. This machine requires a 45kw generator.
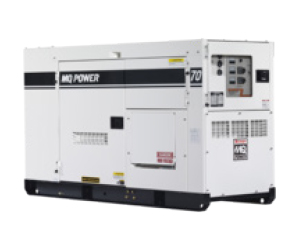
45KW WHISPERWATT GENERATOR
This generator will run rolling units 824-1236 machines. All other machines will need 70KW or 85KW. (pictures not listed)
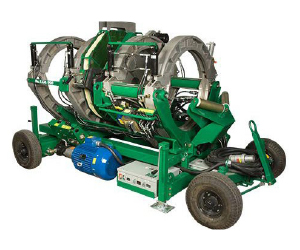
MEGAMC 1236
Fuses 12″ through 36″ pipe.This machine requires a 45kw generator.
Fusion Training and Qualification
Our certified training instructors offer customized classroom instruction and hands on field training programs to successfully train your crew to operate fusion equipment.
Our training meets the operator qualification training standard F3190 set by the American Society for Testing and Materials (ASTM).
Whether your need is for small hand-held HDPE pipe fusion equipment, electrofusion or track and rolling butt fusion equipment, we are ready to train the correct fusion process in accordance with:
- ASTM F2620 (Heat fusion) standards
- ASTM F1290 (Electrofusion) standards
We provide qualification training on the following HDPE pipe fusion methods:
- Butt fusion
- Electrofusion
- Socket fusion
- Hot tapping techniques
Fusion Specifications
Our fabrication process certifies the referenced materials’ conformance to the following standards and specifications:
ASTM F714
Standard specification for polyethylene (PE) plastic pipe (SDR-PR). Based on outside diameter.
ASTM F2206
Specification for fabricated fittings of Butt-fused polyethylene plastic pipe, fittings, sheetrock plate stock or block stock.
ASTM D3350
Standard specification for polyethylene (PE) plastic pipe and fittings material
ASTM D3035
Standard specification for polyethylene (PE) plastic pipe (SDR-PR). Based on controlled outside diameter.
ASTM D3261
Standard specification for butt-heat fusion (PE) plastic fitting for polyethylene plastic pipe and tubing.
AWWA C901
Polyethylene (PE) pressure pipe and tubing, 3/4 in. (19mm) through 3 in. (76mm) for water service.
AWWA C906
Polyethylene (PE) pressure pipe and fittings, 4 in. (100mm) through 65 in. (1,650mm) for waterworks.
ASTM F3190
Standard practice for heat fusion equipment (HFE) operator qualification on polyethylene (PE) and polyamide (PA) pipe and fittings.
ASTM F2620
Standard practice for heat fusion joining of polyethylene pipe and fittings.
AWWA C906
Polyethylene (PE) pressure pipe and fittings, 4 in. (100mm) through 65 in. (1,650mm) for waterworks.
ASTM F3190
Standard practice for heat fusion equipment (HFE) operator qualification on polyethylene (PE) and polyamide (PA) pipe and fittings.
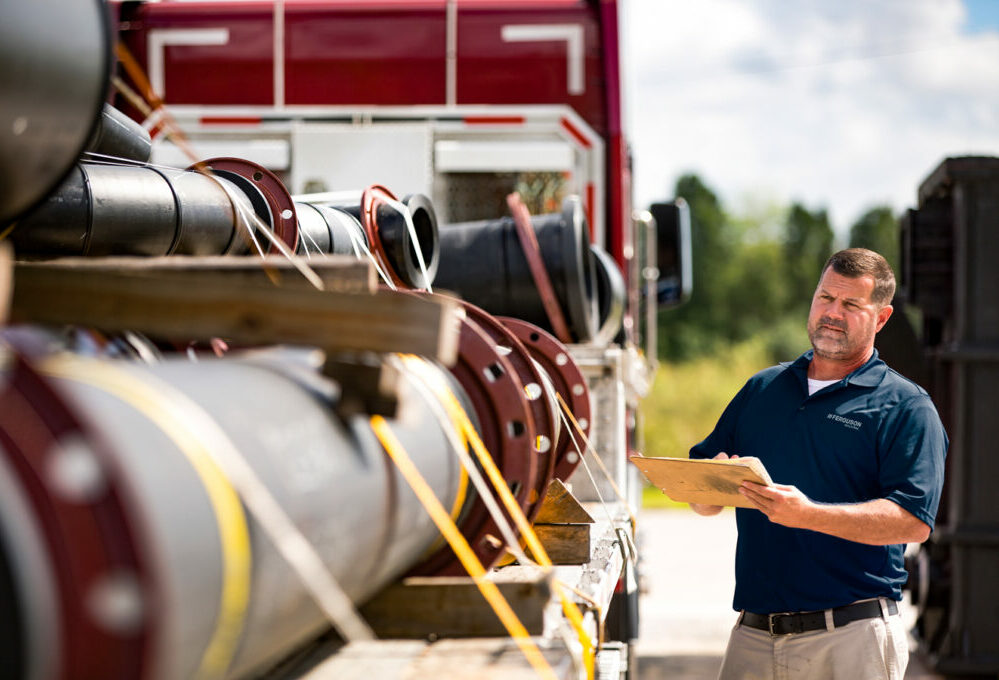
Quality Assurance
Customers trust us because of our commitment to quality. Our HDPE Quality Process consists of several elements to ensure our customers receive the highest quality possible:
Inspection
All pipe and fittings are inspected multiple times throughout the fabrication process. We inspect heat fusion process reports, wall thickness, manufactured angles and cosmetic issues to ensure all the products meet specifications.
Traceability
A unique serial number is heat stamped for traceability on all fittings. Every fitting has a quality record available proving it was inspected and meets all standards.
Data-Logging
A standard procedure used for all fabricated fittings and specialty products to record all the critical data points during the fusing process.
HDPE Capabilities
Nonmetallic Support/Hanging System Flyer
Corrosion-resistant pipe deserves corrosion-resistant support. Our offering of Industrial Thermoplastic products includes an engineered, nonmetallic strut/clamping/hanging pipe support system.
Industrial Plastics Brochure
Piping made from polyethylene is a long-lasting, cost-effective solution for a broad range of piping problems in industrial, marine, mining, landfill, and agricultural applications. Download our HDPE Pipe, Fabrication, and Fusion Services Brochure.
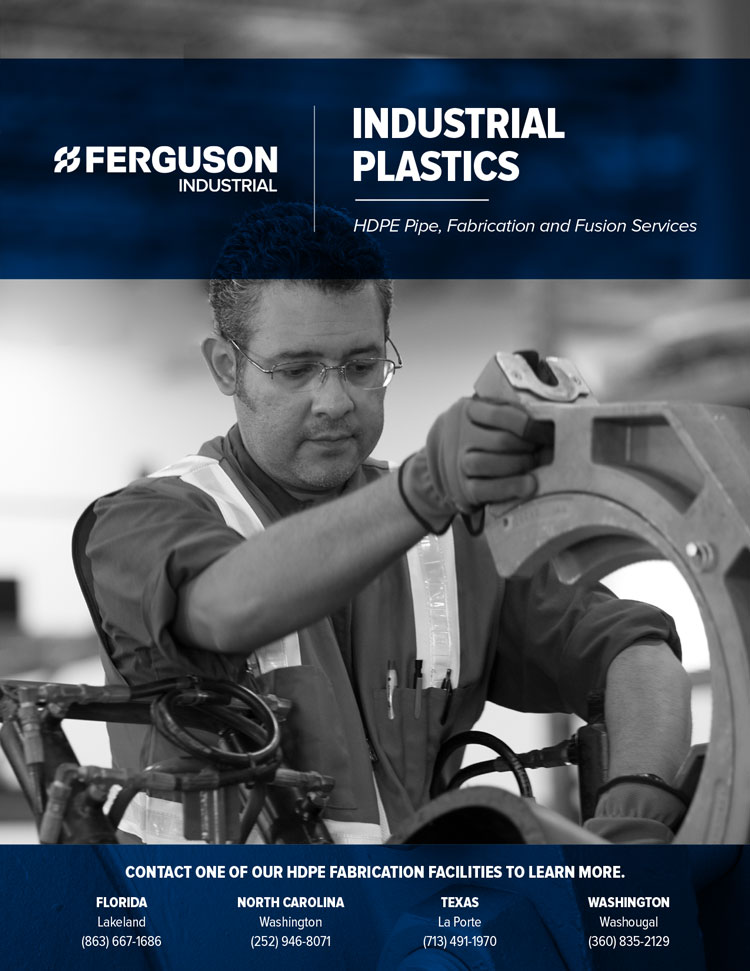